LyoPilot D Series Freeze Dryer
Advanced system technology
1. 2-chamber systems
- Optimal vapor transport.
- Standard side-opening ice condenser for easier observation and cleaning.
- Ultra-low pressure drop between the two chambers.
- Excellent drying rates for sensitive materials and products with low eutectic points or low collapse temperatures.
- Intermediate valve for determining the transition from primary to secondary drying phase.

2. Choose the system fits your application best!

3. Silicone heat transfer fluid shelves
- Equipped with stainless steel shelf areas with silicone heat transfer fluid, providing excellent thermal conductivity.
- The accuracy of different layers and a same layer is within 1°C.
- Hydraulic stopper system, rising from bottom to top and easy for cleaning (available for LyoPilot D8S/LyoPilot D12S)
Design features
1. Minimal space requirements
Compact design with highly efficient and economical operation.
2.Precise temperature and vacuum control
- Precise Temperature and Vacuum Control Thanks to independently developed adaptive PID algorithms, the equipment achieves higher precision in temperature and vacuum control.
- The 10mm thick stainless steel silicone oil shelf ensures a temperature difference of 1°C.
- The ASV adaptive gas injection system, achieving a vacuum control accuracy of up to 0.002 mbar.
3.Comprehensive online analysis tools
Equipped with advanced tools, providing clearer and more intuitive control over the freeze-drying process:
- Eutectic point testing
- Resistivity monitoring
- Pressure rise test
- Pressure comparison method (optional)
- Flash nucleation technology (optional)
4. Outstanding refrigeration system
- Ice condenser: 2-compressor cascade system, ice condenser temperature reaches -90°C.
- Shelf: pulse-type electronic expansion valve, featuring a wide regulation range, quick and precise control on shelf temperature, and low energy consumption.
- PT100 sensor makes the temperature accuracy 1°C.
5. Efficient & convenient ice condenser:
- Internal ice condenser, condenser coil contacts vapor directly, for easier vapor capturing and lower energy
consumption.
- Standard hot gas defrosting, enables customers to quickly proceed to the next freeze-drying process.
- Mechanism door lock of ice condenser, for convenient cleaning.
6. Stoppering function (available for LyoPilot D8S/LyoPilot D12S)
The fully hydraulic automatic stoppering system operates from bottom to top, saving time and facilitating cleaning.
Unique system controller LyoSMART+
LyoSMART+ system controller make an easy-to-use and intuitive user interface.
All of the extensive accessories are also integrated. Reproducible results are assured by automatic process sequences.
1. Convenient and intuitive
- Color touchscreen with clear display.
- Automatic or manual mode optional.
- Intuitive program entry, using various freeze-drying sequences and recipes.
- Memory space for 30 user-defined programs with 36 steps.
- Real-time freezing drying diagram display, selective parameter display, data query & export.
- The main interface is clear and concise, facilitating program editing and operation.
- The control system can set safety values such as vacuum level and resistivity for process feedback control.
- Password protection for startup and lock screen protection when operator is away during processing.
- Equipped with USB port & RS232 port.
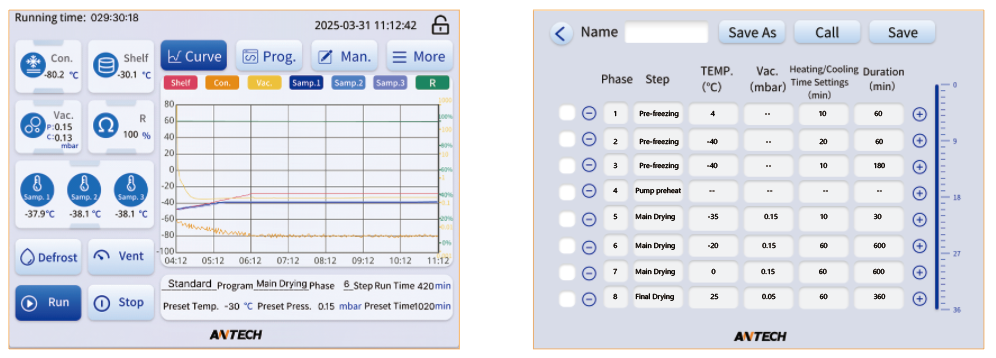
Smart solutions for optimal process observation
1. Freezing point determination
- The LyoTR sensor temperature & resitance combined monitors both electrical resistance and product temperature. From the curves of both of these variables, you can determine the eutectic point and freezing point of your product.
- Our LyoSOFT software and LyoSMART+ makes this possible. The LyoTR sensor allows automated control of the energy supply to the shelves during the main drying phase, so you can avoid critical temperatures during the main drying phase. This reduces the risk of defrosting effects on the product.
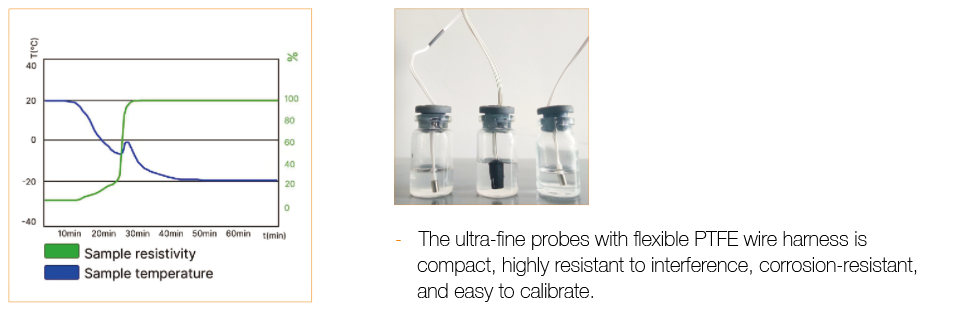
2. Pressure rise test
- The pressure rise test is achieved through the design of the intermediate valve between the drying chamber and the ice condenser. During the drying process, this valve is closed to measure the pressure increase in the drying chamber over a defined time period, which serves as a key indicator for determining the freezing point.
- Typically, the pressure rise rate at the end of main drying should within 0.01 mbar/min. The accurate vacuum control is critical for this function. Thanks to Antech's ultra-high accurate ASV (Advanced Smart Valve) vacuum control, our pressure rise test delivers superior reliability.
3. Pre-vacuum and micro-negative pressure stoppering
- The range accuracy of the traditional Pirani vacuum gauge is limited.Pirani data is not available at higher ranges (10-1000mbar). We can add a silicon crystal vacuum gauge to supplement the measurement and control of this part of the range.
- After putting the sample into the machine, you can first set a rough vacuum degree of 600-950mbar for the
airtightness check of the equipment to ensure that the machine is in a good airtight condition and to prevent
airtightness problems caused by too low temperature, which leads to vacuum abnormalities.
- After the freeze-drying is completed, a higher vacuum degree of 500-800mbar can also be set. The equipment
can backfill the inert gas according to the set value, so that the vial can be plugged under a slightly negative
pressure, thereby ensuring that the dried sample can be stored for a longer time.
4. Comparative pressure measurement(Optional)
- The end of the main drying phase can be detected by using two different vacuum measurement sensors (Pirani gauge and capacitive sensor).
- When the difference between the pressure measurements falls below a preselected threshold, final drying is started automatically.
5.Instantaneous Co-Crystallization system
- Due to thermodynamic factors, the crystallization process of samples within the same batch is not synchronized but random. Variations in supercooling time lead to differences in crystal structure, resulting in inconsistent freeze-drying outcomes (e.g., moisture residue, appearance, etc.).
- The instantaneous crystallization technology can integrate vacuum changes in the cold trap chamber and sample chamber, enabling sudden condensation of samples through controlled vacuum adjustments. Unlike other ice fog-induced nucleation methods, our instantaneous crystallization technology does not require additional auxiliary devices or exogenous substances, even when handling small-scale sample tests.